Lean Manufacturing Process Sample Assignment
Executive Summary
Lean manufacturing process is the process which is implemented by the manufacturing units in order to increase the competitive advantage. The lean operation focuses on the elimination of wastes which are termed by Taichii Ohno of Toyota Motor Company. Apart from seven deadly wastes of Ohno another approach that is used in lean operations is the usage of 5S's as they improve the overall operations of the manufacturing units. Since the lean operations are implemented in almost all the manufacturing units, hence they faced both the success as well as the failure. Toyota Motor Company and Pratt and Whitney Aircrafts are the two companies whose implementation process is been examined and reported.
Ohno's seven wastes in operations
According to Taiichi Ohno of Toyota Motor Company (Womack, J. P. & Jones, D. T. (1996), following are the seven deadly wastes :
1. Overproduction: Ohno believed that this is one of the most serious wastes because it was the main problem. According to Ohno production of materials more than the immediate requirement for use is one of the wastes.
2. Delay/Waiting: Another waste is the delay or gap between the end of the process and the start of another activity or process. (Womack, J. P. & Jones, D. T. (1996) It hinders the work flow and it occurs whenever time is not used efficiently.
3. Transportation/Conveyance: movement of materials, products and information without been necessary. Too much of handling is also inviting risks of damage and decline. I can’t be eliminated however can be reduced with continuous efforts.
4. Motion: he also considered that the movement of people in the form of walking, talking, stretching and reaching is also unnecessary. (Liker, J.K. 2004). Movements of employees to get material or tools can lead to problems.
5. Inventory: Exceeding the requirement in the form of finished goods, raw material or work in progress in order to meet the needs of the customer on time (Womack, J. P. & Jones, D. T. (1996) and to maintain the stability of the product. It decreases the ability to identify the problems quickly.
6. Over-processing: More energy or activity or more value is used and added respectively in order to make the product than the agreed standard.
7. Defects/Correction: Production resulting in the rework or scrap. Defects can cost money.
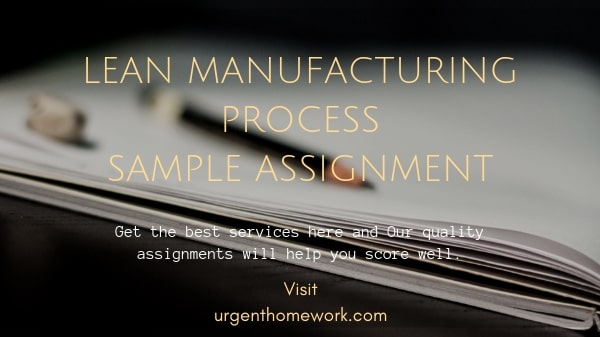
5S's use in lean Operations
The 5S's of lean manufacturing are the most influential parts of lean manufacturing (Schonberger, R. J. (1996), the advantage is that it improves the operations and also starts to change the culture. It is something that every company wants to use. The 5S's are used in lean to support in organisation of the manufacturing. The 5S's are Japanese and are:
Seiri or Sort – The work should be organised in such a way that it is easy to find it. If one will use the batches in small number, it will make the sorting easy and one can find what is required to be found and whenever required. It is very often that people can’t find things if they are not properly sorted. (Womack, James P., Jones, Daniel T. and Roos, Daniel, 1990). It makes it more difficult to find the work or the thing from the pile of materials or the stack of paper. Also, lot of time is consumed in searching for the particular material and it can affect the work.
Seiton or Set to order – One should put the material in a synchronized order and in a manner they are going to use it. Most of the work done is in a sequential manner therefore the material should be organised in such a way that one did not have to go back and forth to find the needed material. This will save lot of time and one can do the work more efficiently. Also, synchronised and sequenced work helps a lot in day to day work.
Seison or Shine – It is very true that if one will fork in a dirty and sloppy environment he or she will be less efficient as there will not be enough space to work or finish the task. And if one will work in a neat and tidy work place or work area, he or she will work faster and will be more efficient and would be able to meet the deadlines. (Holweg, M. 2007). If the work area is clean one is always happy, organised and efficient and can do much more work in the given time.
Seiketsu or Standardize – It is important to have standard operating procedures for the things you know how to do it. It is very important to have standardization at the work place so that all people work in the same manner. It is not the enemy of the world. Standardization helps in doing the excellent work and that what is required at the work place, excellent and efficient work. (Levinson, W., & Rerick, R. (2002). It is important to standardize the work as it helps in training the new people at work place also.
Shitsuke or Sustain – Once the person has sorted the work, set the work in order, made the work place clean and standardized the work, they should also make sure that they put the system in place so that the sustainability is there for the changes made by the person in the work place. Though these changes are positive yet people tend to put them at side.
Critical Analysis of Implementation of Lean Operations in Manufacturing Industry
Lean Operations are used in the manufacturing industry and especially in automotive manufacturing units. Two of the manufacturing units that use this strategy of lean operations are Toyota Motor Company and Pratt and Whitney Aircraft. Taiichi Ohno of Toyota Motor Company developed the standardization of work and also the assembly line. (Liker, J.K. 2004). He was able to innovate the lean process for the company which was termed as Toyota Production System (Holweg, M. 2007) and is actively used and became the part of the manufacturing process. Similarly, Pratt and Whitney Aircrafts also implemented the lean manufacturing to their process and saw the difference in the outcome of the production, which in turn brought huge profits. Both the companies have successfully implemented the lean operation into their manufacturing processes (Schonberger, R. J. (1996) and both of come across seen success as well as the challenges. One of the biggest successes that were seen in Toyota Motor Company was that the people were trained well on the elimination of wastes and also on value of flow of work, which they understood well and implemented. Therefore, the implementation of training and also training the people on key principles is easy. In Toyota Motor Company, it had changed the whole environment culture, as people now are more responsible towards their duties; (Monden, Yasuhiro (1998), they have started thinking out of the box and have the capabilities now to bring change in the attitude. Lean implementation was considered as the key factor in Pratt and Whitney Aircraft for bringing the change in the organisation by bringing the new goals and objective to the company (Crute, V., Ward, Y., Brown, S. & Graves, A. 2003) and managed the time well even when the lean transformation happens. Both the companies that are Toyota Motor Company and Pratt and Whitney Aircraft implemented the lean operations successfully as they were financial sound and therefore they spent money on training programmes and also on consultancies. Also both the companies had a strong leadership as they were able to bring the change in the organisation by improving the work with continuous efforts; this is the reason why Pratt and Whitney aircraft turned into almost double profits in three years time. The management at the Toyota Motor Company were committed fully to implement the lean operations and took all the problems and issues as the opportunity to develop and learn. (Monden, Yasuhiro (1998). That is how the company improved its competitive edge in the market. Other factors that were responsible for the successful implementation of the lean operation in these two companies were the commitment of the managers towards the implementation, belief in the concept of lean operations, (Levinson, W., & Rerick, R. (2002)), employees’ involvement and also the patience to wait for the results which is evident in the Pratt and Whitney company as they started getting the results only after three years of implementation.
The critical analysis of Toyota Motor Company and Pratt and Whitney Aircraft’s implementation have raised the issue of challenges they have met in implementing the lean operations. The decision of meeting the goals can be achieved by either two ways that is make the employees work harder or make them work smarter. However it is found that both the companies have implemented the technique of work harder and because of meeting the goals and the deadlines, employees have worked under extreme pressure (Feld, W. (2000) and stress in order to meet the goals as their working hours were increased. The management of both the companies believed that working harder will gain better results as it will leave no time for any work. They believed in work hard which is to stipulate the working hours and due to this philosophy they lost the opportunity to improve their approach towards the work henceforth the performance in the longer was affected. This trap of capability reduces the chances of any manufacturing unit to increase the productivity as they would not develop the new processes. (Corner, G. (2001). At Pratt and Whitney Aircraft it was noticed that mangers have failed to foresee that due to high pressure during the work, the performances of the employees were affected. The manager’s lack of attribution leads to the high work pressures which demotivated the staff and hence decrease in performance. At Pratt and Whitney Aircrafts mangers failed to understand that the y were in the capability trap however they blamed the staff and the employees for the same.
Another difficulty that was faced by the Toyota Motor Company while implementing the lean operation was to communicate the vision, goals and objectives for doing the same. It was difficult for them to communicate the same thing at all the levels of the organisation. (Shook, J. 2009). Similarly, with Pratt and Whitney Aircraft, though the objectives and vision was communicated to the employees yet they experienced problems while implementing the lean operations. (Crute, V., Ward, Y., Brown, S. & Graves, A. 2003). Due to the implementation, the whole organisation was left in chaos and felt back costly, this happened due to the less experience on the implementing process of lean operations. It is vital for any company to understand the lean operations to the fullest before implementing it. At Toyota Motor Company, it was Taichii Ohno who set the wastes in the operations and also set the standards to lean operations (Liker, J.K. 2004), yet they faced difficulties as people working there were resistant to change the work flow and style of work. The management faced difficulties in convincing the employees about the benefits of the same. Eventually, the employees understood and were convinced of the new approach towards the operations. Also both the companies faced the issue of employees leaving the organisation as they were not able to resist to the change and were not able accept the same. Therefore, implementing the process of lean operation did not come easy for the management as they had to face lot of issues related to the employees in terms of convincing them, training them and coping with them under pressurised situations (Corner, G. (2001).
The lean operation process is a complex process and requires lot of training before the implementation. (Tapping, D., Luyster, T., & Shuker, T. (2002). The complexity of the process starts from the product line but it eventually spreads to the whole organisation. If not properly understood and implemented it can lead to the chaos and also cost lot of money to the organisation. Because of the same, the companies take little longer before they start seeing the profitable results. As said earlier, Pratt and Whitney aircraft took three years to see the positive results this was due to the implementation of lean operations which generally takes more time. Pratt and Whitney Aircrafts also faced the problem of stock keeping while implementing the lean process. (Crute, V., Ward, Y., Brown, S. & Graves, A. 2003). In order to reduce the inventory, they saw only the production process and missed on the product line due to which the process was disturbed and resulted in poor forecasting of material, overproduction, high work pressure and cost increased due to the errors.
Another issue that came across was the mangers faced the challenge of synchronising the requirements and needs of the individuals working in the organisation, organisation and meeting the goals of the organisation. (Tapping, D., Luyster, T., & Shuker, T. (2002). To meet these needs and requirements, manager had to innovate the new techniques for the easy work flow. In the beginning of implementation, employees at Toyota Motor Company were not dedicated to one job and were also not broken in smaller teams to perform the work due to which they faced the difficulties. Later the problem was realised and the smaller teams were built also the employees started working on the rotation basis where the junior engineer does the work (Shook, J. 2009) and later went to the specialist for the skill improvements if required.
Conclusion
The critical analysis of the lean operation’s implementation shows that the implementation process comes with both the advantages and disadvantages. The problems and challenges are faced by the companies who implement this process. The advantages of the implementation of the process is the increased productivity, less wastage, deadlines are met, satisfied customers, however some of the disadvantages are the convincing the employees of the benefits, adaptability of employees to the change, high cost incurred in the training process and people leaving the organisation after the training and in the middle of the implementation process.
References
Corner, G. (2001). Lean manufacturing for the small shop. Dearborn, MI: Society of Manufacturing Engineers
Crute, V., Ward, Y., Brown, S. & Graves, A. 2003, "Implementing Lean in aerospace - challenging the assumptions and understanding the challenges', Technovation, vol. 23, no. 12, pp. 917-928.
Feld, W. (2000). Lean manufacturing: Tools, techniques and how to use them. Boca Raton, FL: St. Lucie Press
Holweg, M. 2007, "The genealogy of lean production', Journal of Operations Management, vol. 25, no. 2, pp. 420-437.
Levinson, W., & Rerick, R. (2002). Lean enterprise: A synergistic approach to minimizing waste. Milwaukee, WI: ASQ Quality Press.
Liker, J.K. 2004, The Toyota way: 14 management principles from the world's greatest manufacturer, McGraw-Hill, New York.
Monden, Yasuhiro (1998), Toyota Production System: An Integrated Approach to Just-in-Time (Third Edition), Engineering & Management Press, Norcross, GA.
Schonberger, R. J. (1996). World Class Manufacturing: The Next Decade. New York: Free Press.
Shook, J. 2009, Applying Lean-er thinking across the enterprise, Lean transformation summit Atlanta [Homepage of Lean Enterprise Institute
Tapping, D., Luyster, T., & Shuker, T. (2002). Value stream management: Eight steps to planning, mapping and sustaining lean improvements. New York, NY: Productivity Press.
Womack, J. P. & Jones, D. T. (1996). Lean Thinking: Banish Waste and Create Wealth in Your Corporation.New York: Simon & Schuster.
Womack, James P., Jones, Daniel T. and Roos, Daniel, (1990), The Machine That Changed The World, Maxwell Macmillan International, New York.
Sample Marketing Assignments
- Banking Industry
- British Airways
- Business Performance
- Business Plan
- Digital Marketing
- Global Market
- Heritage and cultural tourism management
- International Engineering
- Investment decision analysis
- Lean Manufacturing Process
- Woolworth company report
- Market Research Birdie Golfer
- VOLTAMP Company Oman
- Revenue Management
- Risk Management
- Scientific Management
- Stock Market Analysis of BSE
- Tourism Motivation
- Visual Merchandising